Construction firm fined for ignoring fire safety during works
- Development in central Preston was to fit former warehouse with 35 apartments.
- Action taken by both the Health and Safety Executive (HSE) and Lancashire Fire and Rescue Service (LFRS) in multi-agency collaboration.
An Altrincham-based construction company has been fined £165,000 after it repeatedly failed to put in place suitable fire precautions during renovation in Preston.
Glovers Court Ltd were found guilty of four offences in relation to the redevelopment of a former city centre warehouse into 35 apartments spread across six floors. The Glovers Court project was under construction on 16 May 2023 when it was visited by Lancashire Fire and Rescue Service (LFRS). A number of fire safety issues were identified and LFRS prohibited the use of the building, meaning residents already living there had to leave their homes. As construction work was still ongoing, Lancashire Fire and Rescue Service and HSE worked in multi-agency collaboration to deal with this premises.
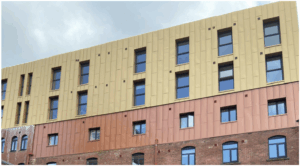
A HSE inspector then visited the site finding the company not to be complying with its duty to ensure suitable fire safety precautions were in place during ongoing construction work. Those failures included:
- No fire detection system;
- No means of raising the alarm in case of a fire;
- Inadequate escape plans; and
- Construction work had not been phased to ensure fire compartmentation was maintained throughout the project to prevent fire spreading to all floors.
As a result of the findings, HSE served a prohibition notice against Glovers Court Ltd, stopping all further work on the property until adequate fire precautions were in place. HSE also served an improvement notice requiring the company to design and implement a fire management plan.
However, during further visits in June and November 2023, HSE found construction work had been ongoing while no action had been taken to comply with either of the notices.
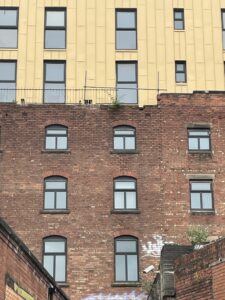
HSE legislation requires a suitable and sufficient fire risk assessment to be carried out by a responsible person. HSE guidance says, where necessary in the interests of the health or safety of a person on a construction site, suitable and sufficient fire-fighting equipment and fire detection and alarm systems must be provided and located in suitable places. Further details on this can be found https://www.legislation.gov.uk/uksi/2015/51/regulation/32/mad and https://www.hse.gov.uk/pubns/priced/hsg168.pdf.
Glovers Court Ltd, of Kingsway, Altrincham, Cheshire, who have now gone into liquidation, were found guilty of breaching:
- 33(1)(c) HSWA by virtue of breaching Reg 11(1) CDM 2015
Reg 11 (1) CDM The PD must plan, manage and monitor the pre-construction phase and co-ordinate health and safety matters to ensure, so far as reasonably practicable, the project is carried out without risks to health and safety.
- 33(1)(c) HSWA by virtue of breaching Reg 13(1) CDM 2015
Construction (Design and Management) Regulations 2015, Regulation 13(1). The failures relating to general and process fire precautions can be identified in the failure to plan, manage and monitor the construction phase to ensure it is carried out without risks and by virtue of Reg 16 (1) &(2) and Part 4 because construction work is being carried out.
- 33(1)(g) HSWA x 2
It is an offence for a person to contravene any requirement or prohibition imposed by an improvement notice or a prohibition notice (including any such notice as modified on appeal).
The company was found guilty in their absence following a trial at Preston Magistrates’ Court on 26 June 2025. They were fined £165,000 and ordered to pay £10,512 in costs.
HSE inspector Christine McGlynn said “This company showed a blatant disregard to both fire safety and the laws in place to protect both people and places.
“Each year there are estimated to be hundreds of fires on construction sites, potentially putting the lives of workers and members of the public at risk.
“Any outbreak of fire threatens the safety of those on site and is costly in terms of its damage and delay. Many can be avoided by careful planning and control of work activities.”
A spokesperson for Lancashire Fire and Rescue Service added: “This prosecution highlights the positive outcomes multi agency working has for fire safety in Lancashire.
“It also highlights the critical importance property developers, owners and managers must give to fire safety.
“We welcome the court’s recognition of the seriousness of these breaches and hope this serves as a clear message to all about their legal and moral responsibilities.”
The HSE prosecution was brought by enforcement lawyer Karen Park and Paralegal Rebecca Withell.
Further information:
- The Health and Safety Executive (HSE) is Britain’s national regulator for workplace health and safety. We are dedicated to protecting people and places, and helping everyone lead safer and healthier lives.
- More information about the legislation referred to in this case is available.
- Further details on the latest HSE news releases is available.
- HSE does not pass sentences, set guidelines or collect any fines imposed. Relevant sentencing guidelines must be followed unless the court is satisfied that it would be contrary to the interests of justice to do so. The sentencing guidelines for health and safety offences can be found here.