Grocery wholesaler fined £1 million after worker killed by reversing HGV
A London-based grocery supplier has been fined £1 million after a worker was killed by a reversing HGV during a delivery in Manchester.
Lee Warburton, 53, a father of three from Stockport, was employed by Bestway Northern Limited, a wholesale supplier serving independent supermarkets across Britain, when the incident occurred.
On 19 February 2019, Mr Warburton and a colleague were making a delivery to a store in central Manchester. He was acting as a banksman, directing his colleague who was reversing the HGV. While attempting to guide the vehicle into the unloading area, Mr Warburton became trapped between the vehicle and a wall. He sustained fatal crush injuries.
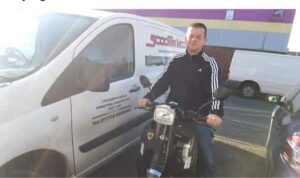
Lee Warburton’s partner, Hayley Tomlinson, described the day he died as the worst of her life. “To be taken in such a cruel manner made it even harder,” she said. “Knowing the pain and fear Lee must have gone through was unbearable. But nothing compares to the moment I had to tell our children their daddy was never coming home.”
She spoke of the long-term impact on their daughters, who were just nine and ten at the time. Both have suffered serious mental health challenges, including depression, bullying and social isolation. “It broke my children’s spirits; they lost the sparkle in their eyes,” she said. “Lee was their hero.”
“My children will miss out on all the milestones Lee should have been here for – walking them down the aisle, meeting their first child. They miss the cuddles, the love he showed them, the days out. This has changed our lives forever.”
A Health and Safety Executive (HSE) investigation found that Bestway Northern Limited, of Abbey Road, Park Royal, London, had failed to implement a safe system of work for vehicle movements. The company also failed to adequately assess the risks involved in the task or provide sufficient training for employees acting as banksmen.
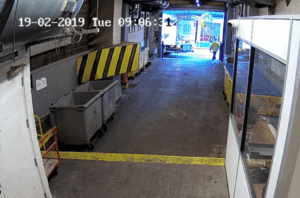
HSE provides free guidance to employers at hse.gov.uk including specific guidance on workplace transport and reversing – Reversing – HSE.
Bestway Northern Limited pleaded guilty to breaching regulation 2(1) of the Health and Safety at Work etc Act 1974. The company was fined £1 million and ordered to pay full prosecution costs of £11,950.07 at a hearing at Manchester Magistrates’ Court on Friday 18 July 2025.
After the hearing, HSE inspector Jane Carroll said:
“The company had failed to implement a safe system of work for its delivery and unloading activities, thereby exposing employees and others to the risk of being struck or caught by workplace vehicles.
“Nearly a quarter of all deaths involving workplace transport occur during reversing, most of which can be avoided by taking simple precautions.
“All work settings involving vehicles need to consider the risks arising from their use and implement adequate measures to ensure the safety of those involved in these activities.”
The prosecution was supported by HSE enforcement lawyer Chloe Ward and paralegal officer Rebecca Whithell.
Further information:
- The Health and Safety Executive (HSE) is Britain’s national regulator for workplace health and safety. We prevent work-related death, injury and ill health through regulatory actions that range from influencing behaviours across whole industry sectors through to targeted interventions on individual businesses. These activities are supported by globally recognised scientific expertise. hse.gov.uk
- More about the legislation referred to in this case can be found at: legislation.gov.uk
- HSE news releases are available at: hse.gov.uk
- Guidance for working safely with vehicles can be found at: Workplace transport – HSE