Company fined £2.5m following uncontrolled acid releases
- Schools were closed following hydrochloric acid release
- Joint investigation and prosecution by HSE and the Environment Agency
- Guidance is available on maintaining equipment in large chemical plants
A chemical manufacturing company has been fined £2.5m following two incidents of uncontrolled releases of highly corrosive acids at its site in West Thurrock, Essex.
Industrial Chemicals Ltd pleaded guilty following the incidents in 2020, one of which caused the release of a hydrogen chloride gas cloud that resulted in schools in the area to close.
The first incident on 6 January 2020 resulted in an uncontrolled release of hydrochloric acid from three chemical storage tanks.
Three hundred thousand litres of the substance was released via poorly maintained pipework. As it came into contact with the atmosphere, this created a hydrogen chloride gas cloud which spread to nearby towns. Nearby CCTV footage shows the atmosphere being engulfed in the cloud within 60 seconds.
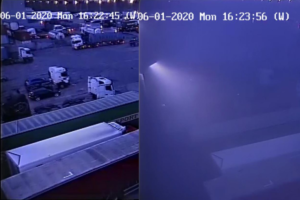
Local businesses were affected and schools in West Thurrock and Chafford Hundred were advised to close. Due to the risk to local residents of exposure to the migrating fumes, advice was provided by emergency responders to close windows and doors.
Hydrochloric acid is highly corrosive and hydrogen chloride is a toxic gas. The incident lasted approximately 24 hours.
On 29 August 2020 another uncontrolled release, this time of sulphuric acid, occurred due to a crack in a pipe. This resulted in the release of 87 cubic metres of sulphuric acid being released into the atmosphere. The valve that was designed to control leaks in the event of cracks did not operate as intended, leading to the uncontrolled release, increasing the risks to operators and delivery drivers.
Sulphuric acid is highly corrosive and can cause lung damage if high levels are breathed in.
A joint investigation by the Health and Safety Executive (HSE) and Environment Agency (EA) into the release of the hydrochloric acid in January 2020 found that pipework had not been installed, maintained and inspected sufficiently which led to several smaller pipe failures before the more serious loss of containment. The investigation found that pipework had not been properly maintained, and a protective chemical-resistant coating had not been applied to the full height of containment walls.
An investigation by HSE into the release of sulphuric acid in August 2020 identified a lack of inspection and maintenance of the pipework and valves. The leak continued for a further two days due to the inability to operate a manual valve to stop the process. The loss of containment was eventually stopped on 31 August 2020. Fortunately, no one was harmed.
Both HSE and industry guidance highlight that work equipment must be maintained in efficient working order and in good repair. Work equipment includes the defective valve and pipework at the site. Suitable and sufficient inspection and maintenance regimes for pipework and valves significantly reduces the likelihood of the loss of containment of dangerous substances to protect both employees, other workers and members of the public from potential harm.
In relation to the January 2020 incident:
- Industrial Chemicals Limited of Old Power Station site, Stoneness Road, West Thurrock, Grays, Essex, pleaded guilty to breaching Section 2(1) and 3(1) of the Health and Safety at Work etc Act 1974 for the loss of containment of hydrochloric acid.
- Industrial Chemicals Limited also pleaded guilty to two charges of breaching environmental permit conditions in contravention of regulation 38(2) of the Environmental Permitting (England and Wales) Regulations 2016 in that the company did not take appropriate measures to minimise the risk of unauthorised emissions of hydrochloric acid/acid fumes to air and land with the potential to impact receptors offsite including the local community.
In relation to the August 2020 incident:
- Industrial Chemicals Limited pleaded guilty to Section 2(1) of the Health and Safety at Work etc Act 1974.
In a hearing at Westminster Combined Court last week (Friday 28 March), the company was fined £2.4 million in relation to charges under the Health and Safety at Work Act 1974 and a further £100,000 in relation to charges under the Environmental Permitting (England and Wales) Regulations 2016.
HSE principal inspector Maria Strangward said: “The uncontrolled release of significant quantities of hazardous substances in these cases was entirely avoidable.
“An appropriate planned maintenance programme should have been in place to ensure that pipes do not fail, and valves operate. The proactive maintenance of pipework and safety critical valves is extremely important at sites such as these.
“Industrial Chemicals Limited’s West Thurrock site is classified as an upper tier site under the Control of Major Accident Regulations 2015, so that businesses and communities are protected, and potential major accidents avoided.”
Adrian Sherman, Environment Agency regulatory officer, said: “The Environment Agency takes its regulatory responsibilities seriously to protect communities and the environment.
“We expect businesses to comply with their environmental permits and will take appropriate enforcement action when they fail to do so. In this case, an appropriate inspection and maintenance programme could have prevented an environmental and public health risk.”
The HSE prosecution was brought by enforcement lawyer Samantha Wells, who said: “At the sentencing hearing the judge noted the previous history of poor health and safety standards by this defendant, which included previous incidents relating to poor maintenance of pipework at this site showing a careless attitude to health and safety which was treated as an aggravating factor which uplifted the sentence imposed.”
The EA prosecution was brought by EA lawyer Laura King.
Further information:
- The Health and Safety Executive (HSE) is Britain’s national regulator for workplace health and safety. We are dedicated to protecting people and places, and helping everyone lead safer and healthier lives.
- More information about the legislation referred to in this case is available.
- Further details on the latest HSE news releases is available.
- Relevant guidance can be found at: Safe use of work equipment. Provision and Use of Work Equipment Regulations 1998. Approved Code of Practice and guidance – L22 and A guide to the Control of Major Accident Hazards Regulations (COMAH) 2015 – L111
- HSE does not pass sentences, set guidelines or collect any fines imposed. Relevant sentencing guidelines must be followed unless the court is satisfied that it would be contrary to the interests of justice to do so. The sentencing guidelines for health and safety offences can be found here.
About the Environment Agency:
- The Environment Agency is a non-departmental public body, sponsored by the Department for Environment, Food and Rural Affairs.
- We work with businesses to help them comply with environmental regulations. Where businesses fail to meet their obligations, the Environment Agency takes appropriate enforcement action, ranging from guidance and advice to prosecution. Our enforcement work helps ensure a level playing field for legitimate businesses and prevents environmental harm.
- Industries with potential to pollute must operate under permits with strict conditions to protect the environment and local communities.
- For more information visit www.gov.uk/environment-agency.