Joinery firm fined for failing to protect its workers
- Unannounced visit by Health and Safety Executive (HSE) found failures.
- The company had failed to protect workers from exposure to wood dust.
- They also failed to maintain electrical installations.
A joinery firm in Middlesbrough has been fined £10,000 after an unannounced visit by Britain’s workplace regulator found multiple health and safety breaches.
Inspectors from the Health and Safety Executive (HSE) visited Abbey Joinery and Manufacture Limited at its Worlton Road site on 25 May 2023. During their inspection they identified multiple failings relating to the company’s control of wood dust as well as its maintenance of electrical systems. These failings meant that employees were being unnecessarily exposed to unnecessary risks.
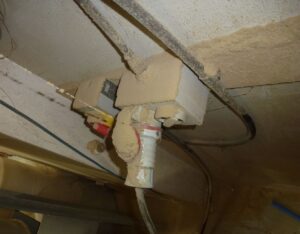
Breathing in wood dust excessively can cause asthma and nasal cancer. HSE provides a range of guidance on working in the woodworking industry, covering the Control of Substances Hazardous to Health (COSHH) Regulations 2002; exposure limits; extraction; and health surveillance.
HSE inspector Darian Dundas said: “Wood dust can cause serious health problems.
“It can cause asthma, which carpenters and joiners are four times more likely to get compared with other UK workers.
“There is clear health and safety guidance available to assist businesses in adequately controlling exposure to wood dust.
“Adequate control of wood dust is achieved when the eight principles of good control practice are applied.”
The HSE inspection also found failures in the company’s electrical installations, including both fixed and portable appliances and machinery. Exposed wiring carried the potential to put workers at risk of serious injury, or worse, from electric shock.
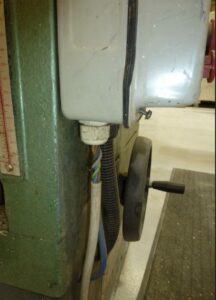
HSE guidance about electrical safety is also available. Darian Dundas continued: “It is vital that maintenance is carried out done to ensure the safety of electrical systems.
“The inspection and testing of equipment is also an essential part of any preventive maintenance programme.
“This investigation was supported by specialist inspectors with a deep knowledge in electrical safety.
Abbey Joinery and Manufacture Limited, of Whorlton Road in Middlesbrough, pleaded guilty to breaching Sections 2(1) of the Health and Safety at Work etc. Act 1974 and was fined £10,000 with £4,428 costs by Teesside Magistrates’ Court.
This HSE prosecution was brought by enforcement lawyer Chloe Ward and paralegal officer Jason Dix.
Further information:
- The Health and Safety Executive (HSE) is Britain’s national regulator for workplace health and safety. We are dedicated to protecting people and places, and helping everyone lead safer and healthier lives.
- More information about the legislation referred to in this case is available.
- Further details on the latest HSE news releases is available.
- HSE does not pass sentences, set guidelines or collect any fines imposed. Relevant sentencing guidelines must be followed unless the court is satisfied that it would be contrary to the interests of justice to do so. The sentencing guidelines for health and safety offences in England and Wales can be found here and for those in Scotland here.
- Relevant HSE guidance referred to in this press release can be found here: Control of substances hazardous to health (Sixth edition) – HSE, EH40/2005 Workplace exposure limits and The Electricity at Work Regulations 1989 – HSE.